Lean
(Improve Velocity, Reduce Waste)
Lean is about creating higher value for customers using lesser resources (space, materials, manpower, equipment etc) to create the value. The objective of Lean is to eliminate all non-value added activities. Any activity or process that consumes resources, adds cost or time without creating value is considered waste and becomes the target for elimination. Lean improves both the effectiveness and efficiency of the organization.
History Of Lean
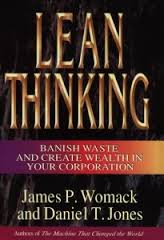
Lean production originated from Japan by Toyota. It is also known as Toyota Production System or TPS. It was developed by Toyota Motor Corporation with the objective to manufacture automobiles with the best quality, lowest cost, and shortest lead time through the elimination of waste.
In 1990’s, Massachusetts Institute of Technology (MIT) researchers Jim Womack and Dan Jones studied the TPS and found that it was a very different approach compared to the traditional mass production method. They concluded that TPS was much more effective and efficient than traditional mass production. They coined the term Lean production to indicate this radically different approach to production.
Their first two books – The Machine That Changed the World (1990) and Lean Thinking (1996) was international best-sellers and in turn, Lean became the revolutionary methodology that changed the world.
The 5 Lean Principles
Jim Womack and Dan Jones contributed greatly to the Lean world by distilling their years of research and study of the Toyota Production System ( TPS) into simple but powerful Lean Principles and Lean tools.
The 5 Lean principles are as follows:
- Value – Specify value from the standpoint of the customer. This is what the customer is willing to pay for.
- Value stream – Identify all the steps in the value stream ( processes), and eliminate any step that does not create value
- Flow – Make the remaining value-creating steps occur in a tight and integrated sequence so the product or service will flow smoothly toward the customer.
- Pull – As flow is introduced, let customers pull value from the next upstream activity.
- Pursue perfection – As these steps lead to greater transparency, enabling further elimination of waste, pursue perfection through continuous improvement.
(Reference: Lean Thinking, James Womack and Daniel Jones, 1996)
Lean is not just about tools
While Lean utilizes a lot of industrial engineering concepts and tools, it must not be thought of as merely a collection of tools to be cherry picked. One of the important aspects of Lean is that it focuses on system-level improvements instead of point improvements.
Instead of fragmented implementation of many projects all over the organization (also known as point improvements) which makes everyone very busy but yet does not add-value to customers, Lean focuses on the critical areas (eg bottlenecks and constraints) identified by the end-to-end process (known as value stream, using a special mapping tool called Value Stream Mapping). In this way, sub-optimization is avoided, resources are deployed in the most effective and efficient way, and the resulting improvement is significant and sustainable.
Successful implementation of Lean requires both the correct deployment of the technical aspects of Lean (Lean principles and tools, also known as Lean hardware) as well as the people aspect of Lean (cultural , mindset and behavioral transformation, also known as Lean software).
Benefits of Lean Implementation
Streamlines processes
Eliminates/ reduces waste or non value add activities
Improves velocity (lead time) – reduces delay and idle time
Reduces cost of operations
Reduces inventory
Improve productivity
Improves customer satisfaction
Improves profits
Application of Lean in different industries and sectors
Lean has been implemented in both the manufacturing and service industries with great success. Some of the industries/ sectors are listed as follows:
Design, research and development (Lean R & D)
Manufacturing ( Lean Manufacturing)
Services (Lean For Service)
Shared service centres (Lean SSC)
Business Process Outsourcing (Lean BPO)
Financial Institutions (Lean for banks, Lean for insurance)
Healthcare (Lean Healthcare)
MRO (Maintenance, Repair & Overhaul) Operations ( Lean MRO)
Public Service and Government (Lean Government)
Educational Institutions (Lean Higher Education)
Logistics (Lean Logistics)
Application of Lean for business processes, office, administration and support processes
Lean is applicable not only to the core processes of both manufacturing & non-manufacturing (services), but also to the office, administration and support processes including:
Sales and marketing
Office and Administration
Finance (eg OTC- Order to cash, PTP- Procure to Pay, RTR – Report to Record)
Kaizen Consulting Group’s Lean Training & Consultancy Services
Check out our Lean training and consultancy services now.
Related pages that you may be interested in: